Rock Export to Lower North Island
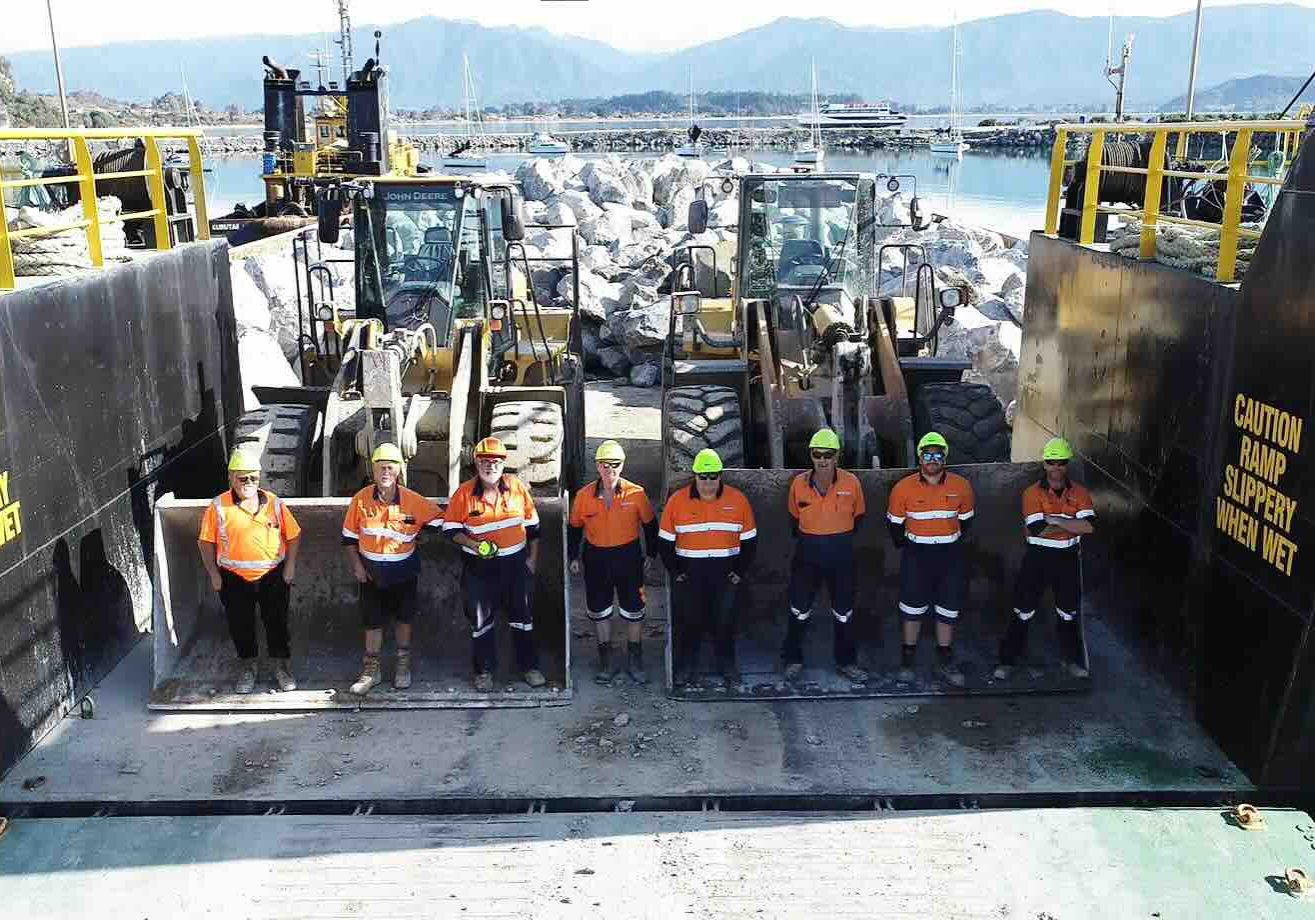
Client: Taylors Contracting
Collaborators: Heron Construction, Port Tarakohe, CentrePort
Key project challenges
- Tight space constraints at Balcks Quarry and Port Tarakohe
- Managing weight distribution as the barge was loaded
- Adapting to continual layout change in the wharf environment
- Strict resource consent constraints for rock size, rock removal and storage of the extracted rock
- Unfavourable weather conditions impacting the barge’s ability to cross via Cook Strait to Wellington
In just 79 working days, 21,263 tonnes of rock was extracted from Taylors’ privately-owned Balcks Quarry to comply with the quarry’s consented three-month annual operating window. Taylors team members commuted from Nelson to the quarry in Golden Bay Mohua each day to undertake the work.
The quarry site itself was extremely constrained for space, so rock had to be extracted and stored offsite until transported to the port. This challenge was exacerbated by the fact that the consent was only for one size range of rock. Everything smaller had to be carted out to an interim dump site. That rock will eventually be returned to the quarry site at the end of the quarry’s life.
The rock export project presented a number of challenges for the Taylors team. The busy Port Tarakohe site needed to accommodate multiple users’ activities during barge loading, including a wharf redevelopment project. Taylors was able to work collaboratively with the owners of the barge, Heron Construction, Sollys, and other Port Tarakohe users to load the barge.
Consent conditions at CentrePort meant that the barge couldn’t be unloaded on a Sunday. However, the majority of the loads were loaded at Port Tarakohe at the weekend. The Taylors team needed to be flexible, managing logbook hours, and making sure that there was enough rock on the wharf ready to load. Team members took days off during the week to accommodate weekend work.
“After the first load we had to slightly change our loading style as we learned more about the optimal weight distribution on the barge, as we could not go past a set water line,” says Quarry Department Manager Ben Burbidge.
“Another level of constraint was added to the site due to the ongoing wharf development work that was underway at the same time. With each load, our work space got smaller and smaller as they moved into our area, and they were also having to rebuild the ramp we were using for every load. I don’t think we used the same ramp twice.”
“We had to be highly adaptive in view of the ever-changing wharf configuration, working in closely with other users. Wharf users worked together to meet everyone’s requirements, and we helped each other to keep everyone’s spaces maximised.
“It’s been a good trial run for potential future opportunities. Thank you to everyone in the Taylors team, both my team and the workshop team, who dropped everything when required to go over to Golden Bay at a moment’s notice to get things sorted so we could keep things moving.”